Machining
With its current capacity, SPE is the leader in the European aftermarket for the production of suspension and steering parts for passenger and light commercial vehicles. By combining advanced technology with experience, the company continues to maintain its success in the industry.
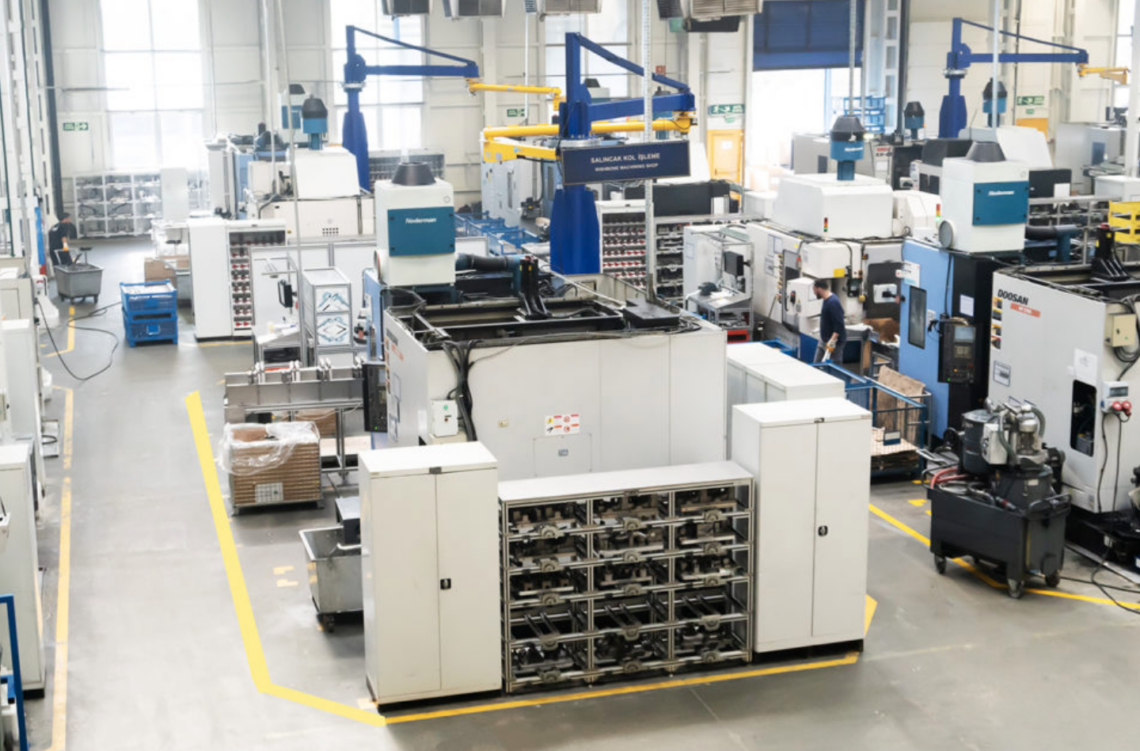
SPE is the leading manufacturer in Europe in product groups such as ball joints, control arms with ball joints, tie rods, tie rod assemblies, tie rod ends, control arms without ball joints, control arm bushings, rubber group components, stabilizer links and bushings, repair kits, sway bar links (Z-links), Z-link kits, stamped control arms, and forged aluminum and steel control arms with ball joints.
With its innovative and technology-driven approach, SPE produces its products using advanced technology, and proudly crowns its success by contributing to the national economy through domestic capital.
Our machining division, which utilizes state-of-the-art CNC machining centers, is committed to producing top-tier components for customers around the world.
Driven by the goal of becoming a global innovation leader in the industry, our division operates with a philosophy of continuous improvement and respect for people. Through extensive training programs, SPE has built a highly skilled, knowledgeable, and innovation-oriented team that consistently delivers high-quality products.
In this process, our company has adopted 5S and other lean manufacturing techniques, and actively applies systems such as Kaizen, Poka-Yoke, and Process FMEA to ensure zero-defect delivery to its business partners.
To guarantee seamless and timely production, we actively utilize ERP (Enterprise Resource Planning) software for planning. Under the scope of visual management, OEE (Overall Equipment Efficiency) metrics are monitored in real time through display panels located on the shop floor.
SPE’s machining equipment park is both advanced and extensive. Approximately 70,000 parts per day—including control arms with ball joints, ball joints, tie rod ends, tie rods, sway bar links, and pitman arms—are produced daily using our CNC machines. In order to achieve this high production capacity and set even greater goals, SPE continues to invest without slowing down.
Link Stabilizer Product Group
Our Link Stabilizer product group is set up to produce original equipment equivalent to OEM parts. In addition, we manufacture two different kinds of products. First one we call XD which is stronger and more durable than original part and other is one top locked. Both products are patented to SPE.
Link Stabilizer process consists welding line, ball-pin machining, assembly and packaging. The entire product range has been designed regarding to lean organization and lean manufacturing systems. Besides that, Link Stabilizer Department works according to ISO TS 16949 quality management system, ISO 14001 environmental management system and OHSAS 18001 management system certificates.
Our department has an average production capacity of 36.000 pieces per day. All employees carry on production activities with zero-defect policy.
Welding Line
We have specially produced resistance (projection) welding machines, manual gas gauges and special gas gauge automation machine at welding process.
In the welding process, link stabilizer housing which are produced at machining or cold forging are welded to shafts which are machined at special bench using electrical resistance welding method.
Assembly and Packaging Line
Link Stabilizer assembly and packaging lines are operated on conveyor with the cell production logic and consist of ultrasonic melting, bushing press and aluminum production lines. The daily capacity is 36.000 pieces and it has the ability to assemble parts according to the special requirements of the customers.
Ball Pin Processing and Galling
Ball Pin is manufactured in our processing line with specially manufactured double-headed lathe and automatic lathe turning machines, followed by special galling benches and polishing of the tooth and sphere parts. According to the customer request, all ball pins produced can be checked with the camera system by dimensional control and crack control by Eddy-Current method.
The daily capacity of our ball pin processing line is 90.000 pieces and it can serve all product groups (Ball Joint-Tie Rod End, Control Arm, Wishbone and Link Stabilizer) in our company.
Ball Joint, Tie Rod End and Inner Tie Rod Product Group
100% quality parts are produced with new full automatic assembly lines. The swing and torque values of the produced parts are the same in each part.
In all lines, molds-apparatus with POKA-YOKE are used. Problems in the processed parts can be detected with the apparatuses. 5S work is being done continuously.
Technological systems that increase productivity are used in all production lines. New systems are constantly being added for faster and better quality production.
Technological machining fixtures and cutting tools are used in machining. With new special machining tools, parts are processed much more quickly with simultaneous operations.
The latest technological clamping systems are used in machining. With the new clamping system, both the work piece and the cutting tool are held correctly. This has resulted in a significant reduction in the use of scrap and cutting tools.
The use of cutting tools and consumables is followed by an automated tool rack on the computer. The operator enters the desired tool into the computer and the corresponding rack automatically comes in front of the employee. This is followed by more efficient use of consumables and inventory tracking.
Employee productivity is increased by using market type shelves in assembly and packaging lines. All products packed with bar coding system are read on 100% system and parcel label is taken automatically.
Control Arm with Ball Joint Product Group
After forging process, majority of the components go through machining at SPE. SPE’s horizontal and vertical machining centers are equipped with high technology clamping and fixing systems resulting in tight tolerances and high speed in machining process for track control arms and wishbones – translating to high quality and competitive cost.
Our OE-trained engineering and manufacturing team utilizes the latest technology in cutting bits and apply the principles of continues improvement to push themselves to the limit.