Cataphoresis
SPE, the leading manufacturer in Europe, produces a wide range of product groups including ball joints, control arms with ball joints, tie rods, tie rod assemblies, tie rod ends, control arms without ball joints, control arm bushings, rubber group components, stabilizer links and bushings, repair kits, sway bar links (Z-links), Z-link kits, stamped control arms, and forged aluminum and steel control arms.
SPE stands out in the industry as a pioneer in implementing environmentally conscious production processes. Aiming to prevent environmental pollution and contribute to the preservation of nature, the company continuously works to minimize pollution caused by waste. Moreover, by using advanced technologies aimed at more efficient use of natural resources, it embraces an eco-friendly manufacturing philosophy.
What is Cataphoresis?
Cataphoresis coating, also known as “Electrochemical Paint Coating,” is an environmentally friendly process due to its closed-loop recovery systems. This method eliminates shape-dependent painting issues often encountered in powder and wet paint applications. Cataphoresis paint ensures consistent corrosion resistance on both the inner and outer surfaces of a part, regardless of its geometry.
The cataphoresis line within SPE is unique in being self-cleaning. The production process is continuously monitored with tests such as the Cross Cut Test (Adhesion Test), Impact Test, and Salt Spray Test (Corrosion Resistance Test). In corrosion testing, a minimum standard of 720 hours is required.
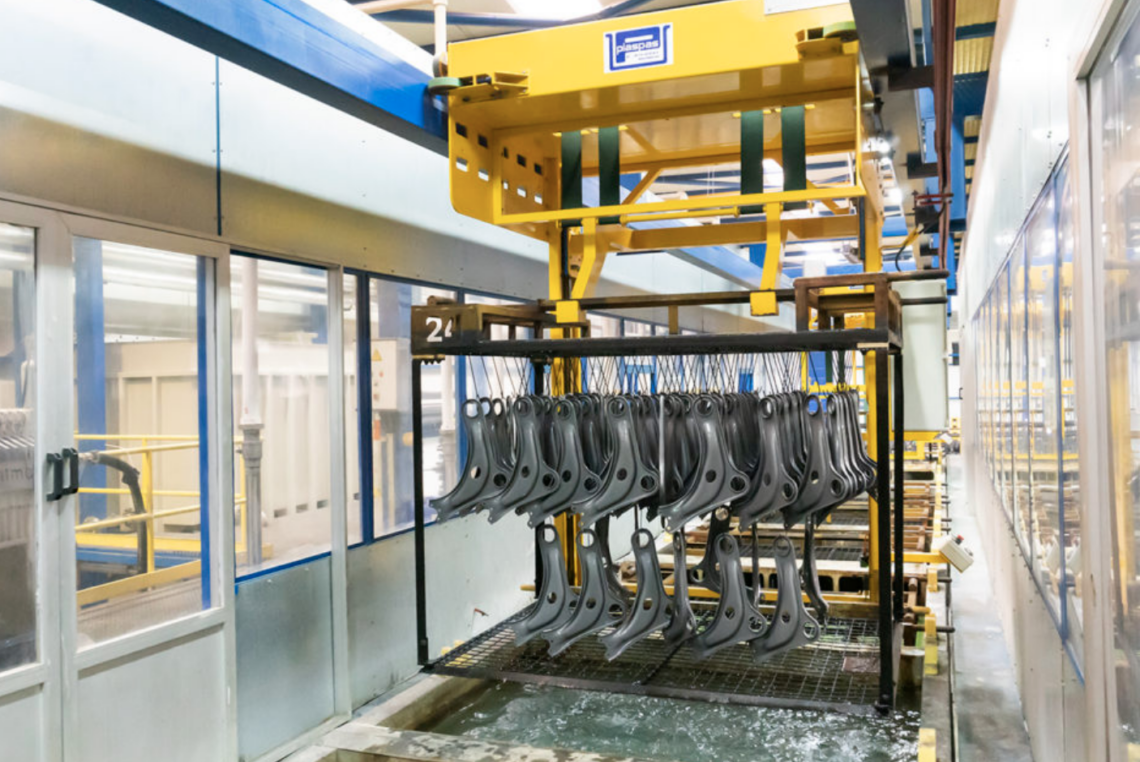
Our products are located in the lower sections of vehicles, which are not visible to the eye, and are classified as safety components. This is a crucial factor that reinforces SPE’s responsibility toward its customers in terms of safety and quality.
Suspension parts operate under constantly changing forces and harsh road conditions such as road salt, rainwater, stone impacts, and friction. Therefore, SPE not only manufactures in compliance with raw material and dimensional standards, but also aims to extend the service life and ensure the quality of its products through the application of cataphoresis coating.
Cataphoresis Coating: A Water-Based and Environmentally Friendly Painting Technology
Cataphoresis coating is a water-based electrochemical paint application method. This technology offers superior protection against corrosion and impact, significantly outperforming traditional methods such as electrostatic powder and electrostatic wet painting.
The cataphoresis line typically consists of closed-loop circulating chemical tanks and operates in integration with auxiliary facilities that are self-feeding and continuously control chemical waste. This system is environmentally friendly, as it significantly reduces the amount of chemical waste. Furthermore, there are no paint losses or airborne particles that could negatively affect the working environment during the painting process, providing a substantial advantage both in terms of environmental impact and operational costs.
Cataphoresis Coating Process
The cataphoresis coating line is composed of four main sections:
1. Surface Cleaning Section
To ensure strong adhesion between the paint and the metal surface, proper cleaning is essential. This section includes degreasing and rinsing tanks, which eliminate contaminants such as oil films, dirt, and dust, allowing for optimal paint adhesion.
2. Surface Preparation Section
This stage prepares the surface for coating by forming ZnPO4 (zinc phosphate) crystals on the metal, enhancing paint bonding. It includes the activation tank, ZnPO4 tank, and DI (deionized water) rinse tanks.
3. Coating Section
This is where the water-based paint is applied to the metal surface. It includes the paint tank and UF (ultrafiltration) tanks, where the coating process is carried out.
4. Flash-Off and Curing Oven Section
In this stage, the liquid components in the paint evaporate and are removed, followed by curing in an oven to harden the paint and ensure long-lasting protection.
SPE’s Cataphoresis Line
At SPE, chemical vapors in the cataphoresis line are treated through a scrubber (gas purification) system. Chemical substances in the vapor are captured, sent back to the treatment facility, and safely disposed of. The cleaned exhaust is released into the atmosphere in an environmentally safe manner. Additionally, heat is recovered from the oven exhaust stack, preventing negative environmental impact.
The hangers used in SPE’s cataphoresis line are specially designed so they do not retain any paint during the coating process, thus eliminating additional cleaning waste. This is a key feature that sets SPE’s cataphoresis line apart. Moreover, all bath parameters are continuously monitored and recorded, enabling constant process optimization and positive feedback.
Testing Performance and Quality Control
SPE continuously tests product quality throughout the cataphoresis coating processes. Tests such as the Cross Cut Test (Adhesion Test), Impact Test, and Salt Spray Test (Corrosion Resistance Test), conducted on sample plates, show that the coating thickness ranges between 18µ and 20µ, and corrosion resistance varies between 720 and 1000 hours.
These test results demonstrate exceptional quality that exceeds OEM (Original Equipment Manufacturer) standards, proving the high durability of SPE’s products.